About Us
From the time where freight forwarding was regarded as a highly potential industry based on economic recovery. Cargomind was incorporated in Malaysia in the year 2008 to venture into this service sector by capitalising its own resources and utilising the expertise and wisdom of its management team.
In its ongoing expansion planning, Cargomind has established branches across Malaysia’s major port and airports to include incorporation of Kargomind Limited, United Kingdom and Kargomind Pte Ltd., Singapore. Cargomind spread its wing into international market with supports from the global freight forwarder networks and affiliates.. Cargomind recently venture into cyber technology with its participant in pioneering Halal Logistics Management System (AIIVA) as part of its movement towards industrial Revolution 4.0
The Management together with its support team are fully committed to provide satisfactory quality services. Cargomind has been certified with ISO 9001:2015 for Quality Management System (QMS) and also awarded a 4 stars rating by SME Corp Malaysia.
VISION
Aspire to be a comprehensive global logistic
service provider of choice by 2025.
MISSION
AEO
Authorised Economic Operator (AEO) in Malaysia.
MTO
To be the first line of logistics provider for Government Agencies and GLC by 2022.
POLICY
To deliver logistics task of projects that meet and exceed client's expectation on.
▷ Schedule
▷ Quality
▷ Safety
▷ Cost
SERVICES
To participate in every sector of logistics.
▷ Strategics Goods
▷ Engineering Process
▷ Special Heavy Movement
▷ Medical Device Specialist
Strategic Direction
History

HEALTH, SAFETY AND ENVIRONMENT POLICY
THIS POLICY IS GOVERNED BY THESE 5 MAIN PRINCIPLES.
Identify the Risks
Identify where, when, why and how events could prevent, degrade, delay or enhance the achievement of the HSE’s objectives. Approaches used to identify risks include checklist, judgement based on experience and records, flow charts, brainstorming, systems analysis, scenario analysis.
Analyse the Risks
Each identified risk should be analysed in terms of:
• the existing controls in place to manage the risk
• likelihood of an incident occurring
• impact to determine the level of risk posed. The impact and likelihood should be assessed using the HSE Risk Assessment Matrix.
In analysing risk it is important to consider not only the issue of minimising risk but also maximising opportunity.
The resultant analysis should be documented in the risk register.
Evaluate the Risks
The purpose of risk evaluation is to make decisions, based on the outcomes of risk analysis, about which risks need treatment and the treatment priorities. This requires comparing estimated levels of risk against the pre-established criteria and then to consider the balance between potential benefits and adverse outcomes for the health service. This enables decisions to be made about the extent and nature of the treatments required and the priorities for the health service.
Treat the Risks
Where risks require further treatment (action) a treatment (action) plan is developed to address it. This plan should outline the specific cost-effective actions to be taken, the person responsible and the timeframe for action. The plan should aim to reduce the level of risk. If possible risks should be eliminated. Where this is not possible, the risk should be reduced to as low a level as is reasonably practical.
Monitor and Review
It is necessary to monitor and review the effectiveness of all steps of the risk management process. This is best achieved through existing management . For each stage of the process records should be kept to enable evidenced based decisions to be documented as part of the process of continual improvement and learning.
A. Elimination
When processes and procedures are being analyzed for risks, it is important to look for ways to eliminate the risk entirely. If you can, you don’t need to create a process or procedure to avoid it. Of all control methods, eliminating a hazard is the most desirable and effective. However, it is often the most difficult to implement, especially for processes that already exist at a facility.
B. Substitution
Substitution means replacing the process or item that causes a hazard with one that does not. For example, replacing a solvent-based degreaser with a citrus-based degreaser is a substitution that reduces air emissions and is typically less harmful to employees and the environment. When considering substitution methods and products, it is important to review them thoroughly to ensure that they do not create new hazards.
C. Administrative Controls
Administrative controls document processes that a company will follow to eliminate hazards and/or minimize employee exposure. Forms of administrative controls include standard operating procedures, established safe work routines, employee training and emergency response drills. They can also include what some might consider “creature comforts,” such as taking frequent breaks when working in extreme heat or cold and rotation of job functions. Although they may seem superfluous, these activities do serve a safety function. Scheduling downtime to perform preventive maintenance and routine inspections can also be directly tied to safety controls, because they minimize the chance for malfunctions that could put employees at risk for injury or death.
D. PPE
When engineering and administrative controls aren’t enough to keep employees safe, the balance of the safety load falls on PPE. Although PPE is a form of protection, it presents its own challenges, including the following:
1. It has to fit correctly to be effective.
A good example of this is respiratory protection. If you can’t get a good seal, it’s not going to work well.
2. It has to be worn.
Yes, you can get a pair of safety glasses for a couple bucks. But if they’re not comfortable, or if they fog up in hot weather s no one wants to wear them, you’re probably wasting your money. They either won’t be worn, or only if someone vigilantly polices each work area to make sure of it. Spending a bit more for glasses that feel better and don’t fog up is a good use of safety funds, even on a tight budget. The same goes for earplugs, safety shoes and everything else that employees need to wear every day.
3. It has to be removed from service when it has passed its prime.
Nothing lasts forever, especially PPE. A frayed fall harness, safety shoes with smooth soles, glasses with severely scratched lenses and gloves with holes—these are all examples of PPE that needs to be replaced immediately.
4. It has to be understood.
Employees need to know about hazards in their workplace and how engineering and administrative controls, in combination with PPE, help them work safely. They also need to be taught how to wear, use and take care of any PPE that they’ve been issued so that it is truly effective and provides that last line of defense against a safety risk.
Eliminating hazards and substituting less hazardous products are not always possible. Retrofitting machines with engineering controls can be expensive. Administrative controls take time from production schedules. G etting everyone to wear their PPE can be a pain. But bringing together all of these elements is the only hope for eliminating the chance of an employee’s duties causing injury, illness or death.
Communicating occupational safety and health information effectively is crucial in preventing employee injuries and illness. Effective safety communication is:
1. Interactive.
It flows both ways. You speak about safety and you listen to employees’ concerns and suggestions.
2. Informative.
It tells employees what they need to know to work safely under all conditions.
3. Positive.
It focuses on the exchange of ideas and information to improve workplace safety and prevent accidents and illness.
4. Productive.
It allows you to interact successfully with employees and spread your safety message to all who need to hear it.
The term incident can be defined as an occurrence, condition, or situation arising in the course of work that resulted in or could have resulted in injuries, illnesses, damage to health, or fatalities.
The term “accident” is also commonly used, and can be defined as an unplanned event that interrupts the completion of an activity, and that may (or may not) include injury or property damage. Some make a distinction between accident and incident. They use the term incident to refer to an unexpected event that did not cause injury or damage that time but had the potential. “Near miss” or “dangerous occurrence” are also terms for an event that could have caused harm but did not.
The term incident is used in some situations and jurisdictions to cover both an “accident” and “incident”. It is argued that the word “accident” implies that the event was related to fate or chance. When the root cause is determined, it is usually found that many events were predictable and could have been prevented if the right actions were taken – making the event not one of fate or chance (thus, the word incident is used). For simplicity, we will now use the term incident to mean all of the above events.
The information that follows is intended to be a general guide for employers, supervisors, health and safety committee members, or members of an incident investigation team. When incidents are investigated, the emphasis should be concentrated on finding the root cause of the incident so you can prevent the event from happening again. The purpose is to find facts that can lead to corrective actions, not to find fault. Always look for deeper causes. Do not simply record the steps of the event.
Reasons to investigate a workplace incident include:
- most importantly, to find out the cause of incidents and to prevent similar incidents in the future.
- to fulfill any legal requirements.
- to determine the cost of an incident.
- to determine compliance with applicable regulations (e.g., occupational health and safety, criminal, etc.).
- to process workers’ compensation claims.
The same principles apply to an inquiry of a minor incident and to the more formal investigation of a serious event. Most importantly, these steps can be used to investigate any situation (e.g., where no incident has occurred … yet) as a way to prevent an incident.
A formal boardroom review of health and safety performance is essential. It allows the board to establish whether the essential health and safety principles – strong and active leadership, worker involvement, and assessment and review – have been embedded in the organisation. It tells you whether your system is effective in managing risk and protecting people.
Core actions
The board should review health and safety performance at least once a year. The review process should:
- examine whether the health and safety policy reflects the organisation’s current priorities, plans and targets;
- examine whether risk management and other health and safety systems have been effectively reporting to the board;
- report health and safety shortcomings, and the effect of all relevant board and management decisions;
- decide actions to address any weaknesses and a system to monitor their implementation;
- consider immediate reviews in the light of major shortcomings or events.
Good practice
The board should review health and safety performance at least once a year. The review process should:
- Performance on health and safety and well-being is increasingly being recorded in organisations’ annual reports to investors and stakeholders.
- Board members can make extra ‘shop floor’ visits to gather information for the formal review. Good health and safety performance can be celebrated at central and local level
Our Network
Cargomind's network is further reinforced via its associations and affiliations within the local, regional, as well as international industry players and authoritative bodies. We offered logistics networking for our clients throught our associates around the world.
LOCAL
- Affiliate Member of Federation of Malaysia Freight Forwarders (FMFF).
- Ordinary Member of Selangor Freight Forwarder and Logistics Association (SFFLA).
- Registered with Malaysia External Trade Development Organization (MATRADE).
INTERNATIONAL
- Member of International Federation of Freight Forwarders Association (FIATA).
- Member of Security Cargo Network (SCN).
CERTIFICATION & ACCREDITATION

The Enterprise 50 (E50) is a prestigious award programme that recognizes the achievements of Malaysia’s enterprising small and medium enterprises (SMEs), which are well positioned for the future. A total of 50 winners are selected based on their financial capabilities, operations and management competencies, among the nominations received.
MEMBER OF
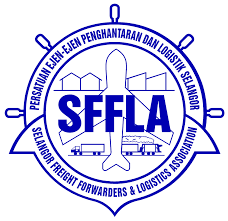
SFFLA (Selangor Freight Forwarders & Logistics Association )
will also undertake to protect members’ interests through a pro-active and consultative approach in mediating and handling disputes and grievances that affect their members.

MFF( Federation of Malaysian Freight Forwarders )
was established in 1987 as a National Logistics Association. In 2000, FMFF was recognised by Malaysia Ministry of Transport

SCN (Security Cargo Network)
is a global alliance of independent international freight forwarders who have joined together to offer superior service to shippers for their cargo at both the origin and destination points.

(FIATA) International Federation of Freight Forwarders Associations
The International Federation of Freight Forwarders Associations is a non-governmental organization representing 40,000 forwarding and logistics companies, employing 8 to 10 million people in 150 countries.